
I’m just going to start calling the new project house in Pikesville “Pikesville”. It makes for shorter post headings.
Last time we checked in over at Pikesville, I was just showing off some early demo pictures. After doing nothing for just short of a month, we’ve had a busy couple of weeks over there. I’ve been working longer days at the office so that I can get an extra day off each week and spend it trying to accomplish things there. My big focus this week was roughing in the electrical for the kitchen and the utility room; the two rooms I gutted earlier.
Before we get into the tangled web of wire, I'll jump in with a disclaimer/warning. I’m not a licensed electrician. I spent a number of years of my time in the Navy doing a lot of very dangerous electrical work on large scale systems, and received training and certification to do those things. So, while I’m not fully up to speed on all the in’s and out’s of the residential electric code, I do keep abreast of it as much as I can. And I will have a licensed electrician take a look at my work before I put up the sheetrock.
One of the first things I did was go around and mark the points where power came into the kitchen from the panel. To do this, I used a no contact voltage tester, like this one.

These things are pretty great. I had to buy a new one, though, because my last one started turning off sporadically, and through a series of unfortunate coincidences, I ended up with a blown breaker and a nervous twitch. Use rubber-handled tools.
Now that I knew where power came into the kitchen, I used a marker and some tape and labeled the hot end of the cable with the circuit number that it corresponded to. During this process, I went to use the bathroom and found that it was without power. This wasn't too surprising, considering the age of the house. I decided to pull the kitchen and utility room out of the existing circuits in the house. To do that, I needed to add some junction boxes on either end of the kitchen and run some new wire through the kitchen ceiling from box to box. Here’s the one I put in on the far end.

When I ripped down the old sheetrock on this wall, I found that the contractor who had renovated the bathroom 5yrs ago had buried a box. See that black metal strap crossing over a patch in the wall? That’s where it was. This is a big no-no. Don’t bury boxes. I decided to put the new junction box where I did so that I could remove that buried box at the same time. So this new box contains the power feed for the bathroom, which used to power half the outlets in the kitchen AND the bathroom.
Here’s the junction box on the entrance half of the kitchen.

Kind of a crappy picture. It was a crappy job, too. The box was already in place, so I had to keep using it. This picture was taken from the kitchen looking up into the rafters. In order to work on this box, I had to crawl along the eves of the house, accessed from upstairs. It was cramped and uncomfortable. If you’ve ever done something like this, the first question you are probably asking is “how many times did you have to get out and back in?” Well, I forgot a tool I needed twice, and I dropped a tool once. I also wanted to be really sure I had the right hot wire to feed the bathroom with, so I got out and triple-checked that. So 4 times crawling in and out. [sigh].
Now that I had isolated the kitchen from the rest of the house’s power, I pulled out all the old outlets and wire runs. It’s a nice moment when you look into the room and have a clean slate to start on. But slates aren't meant to stay clean, so I went around and put in the new boxes for the receptacles and switches that will be going in. This takes a lot of foresight. You need boxes at
certain heights for certain things (like a microwave/range hood, oven, etc), so you have to know where your cabinets and appliances are going to be. This is one of those times where I stand there staring at things for a long time, thinking and rethinking to make sure I get all the details right. I’m sure I’ll forget something, but at least it won’t be a serious thing.
Once all the boxes were in, I ran the cable to each box and switch. Nothing is hot at this point; I’m just setting up the cable runs. This requires a paddle bit and a strong drill to put holes through the studs. Next up is the can lights. I used the same cans I used
when I did my own kitchen lights almost
two years ago(!!) with my dad.

That’s me 30lbs heavier and with (sadly) noticeably darker hair. Come on, now. I’m too young to be saying that.
Quick aside: if you ever EVER gut a room, take pictures of the walls! There will come a day when you need to know where a wire comes from/goes to, and you will be thankful you have those pictures.
These can lights are crazy-easy to install and hook up. They have nice and easy push-in connectors in them, and they come with nails and adjustable rails to fit nice and snug between the ceiling joists. Once they were in, I was pretty much done with the basic rough-in. The outlets above the countertop are all 20-amp, per code. The microwave/range hood has it’s own 20-amp feed, and the lights, dishwasher, and garbage disposal have a 15-amp feed. I ran these to the breaker panel and tried to put in my new breakers, but they didn’t fit.

My thumb is covering most of it, but there is a notch in this breaker. Old Cutler-Hammer panels have this dumb rejection bar to prevent you from using breakers that don’t have this notch. They don’t make breakers like this anymore, though. [sigh]. Cutler-Hammer recommends removing the rejection bar, which is held in with one-way screws and requires taking out the main breaker to get to. I haven’t done that, yet. In the mean time, I’ve..ahem..
borrowed some non-essential circuits (no more outside lighting or upstairs outlets) in order to get my lights working.
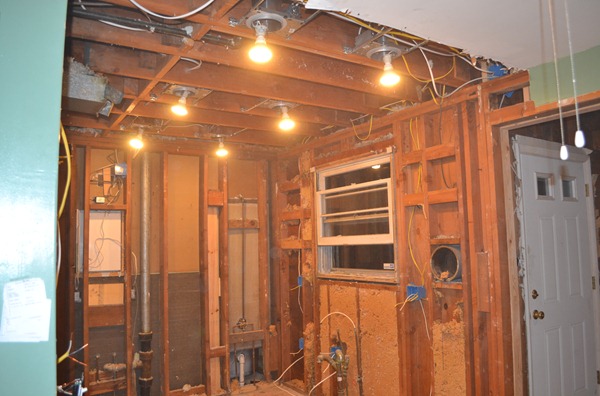
Hooray! I
love this part. New lights are so crisp and change the whole feel of a project when it’s been so dark and depressing for so long. It’s the first
new thing. In that picture, you can see some of the other new stuff.. the two white(14/2) leads under the window are the dishwasher and disposal.. the white line going into the box to the right of the window is for the switch for the disposal. That circle thing is an old vent! It will be coming out soon.
Now that I had most of the rough-in done for the kitchen, it was on to the utility room.

There’s going to be base cabinets and counter top along this back wall of the utility room, so I’ve got some countertop-depth outlets in for that. The lighting in here is also can lights, but the ceiling isn’t deep enough for normal cans. Instead I got these new LED lights.

These things are pretty sweet. They can be used for retrofitting; they’ll fit right inside an existing can light. You can also put them in a standard J-box (a round 4” ceiling box), either new-work or old-work. I put 4 new-work boxes in the ceiling and put one of these lights on each one. Super bright and crisp!
What a mess! That new framing, there, is because we are vaulting the ceiling. The utility room was an addition, so you can see the old roof right there. Neat, huh.
That’s it for now. This week I’m meeting with the electrician to review my work, and also to get him to help me remove the
restriction bar in this box (link is where I learned about what to do) so that I can add the new circuits I need.
So.. anything I might be missing? Any electrical stories of your own? Let me know below! I’ve got a new comment system and I’m anxious to see how it goes over.
PS.. If you’re waiting for the reveal of the flooring project, I’m still working on that. I’ve been trying to get some particular pictures to show my mistakes, but it’s always dark when I try to get them. Stupid short days of winter!